Depending on the requirements profile and the intended purpose, we can produce individually manufactured stamped parts for you.
Whether it’s the shortest, short or long production runs, the results will comply precisely with your specifications down to the smallest detail. With our many years of experience in engineering, we of course also support you in developing prototypes. Our range covers flat seals and gaskets, stamped seals and gaskets, gasket frames and rubber seals in the form of rings and also insulation parts, pieces cut to size, strips or larger plates. Profitability and sustainability are major quality features of our solutions.
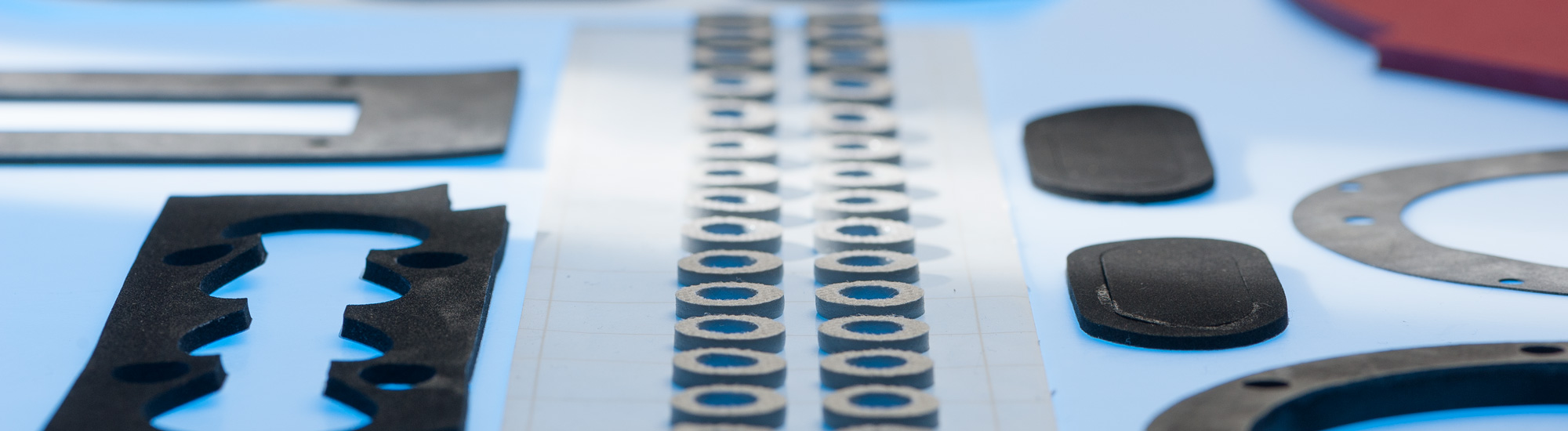
Sealing technology
Variety and precision for every requirement
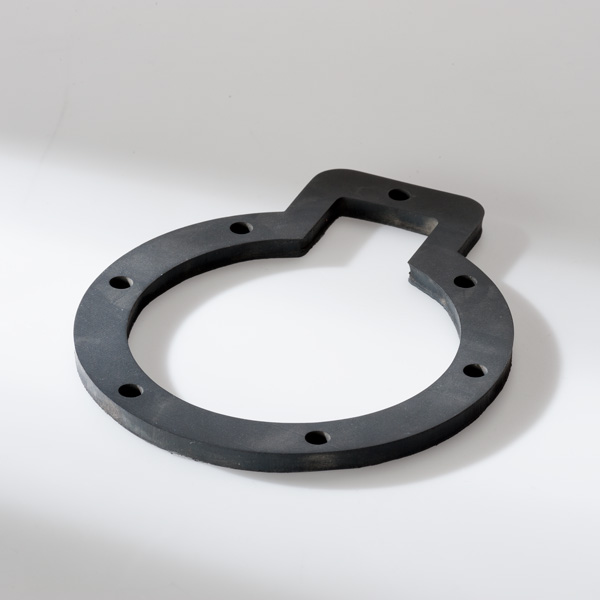

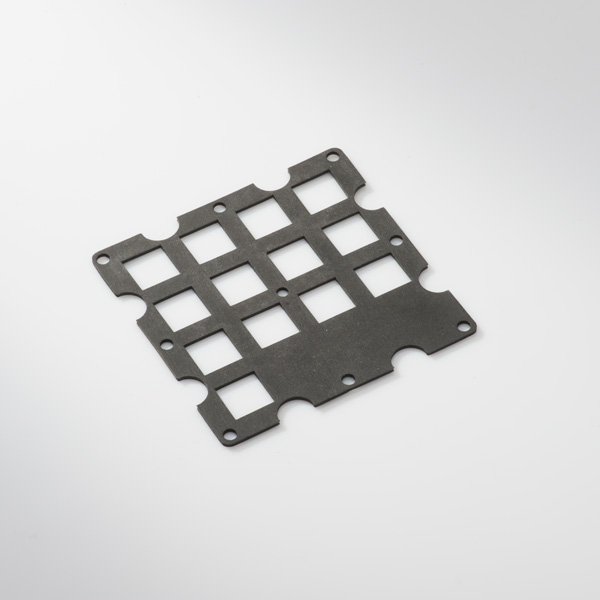
With our modern machinery we have a large number of methods available for the production of stamped parts. In addition to complete cutting, steel strip cutting, sharp cutting and scissor cutting, we also have plotting and water jet cutting.
Depending on the requirement, stamped parts may be manufactured on a CNC press, a swivel arm press, a gantry press or a travelling head press. We will be happy to advise you on the material and the best manufacturing process.
- Stamped parts for insulation, covering, upholstering, damping, as spacers, rattle protection, vibration protection and much more besides.
- The latest production processes, provision of input materials and the option of rapid tool manufacture
- Solutions for all customers’ requirements
- Delivery in the most varied thicknesses and smooth-edged
- Rapid production and delivery of any desired volumes
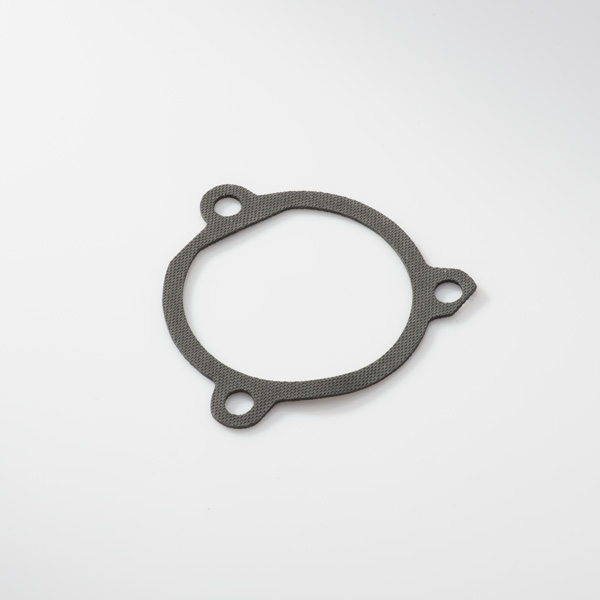
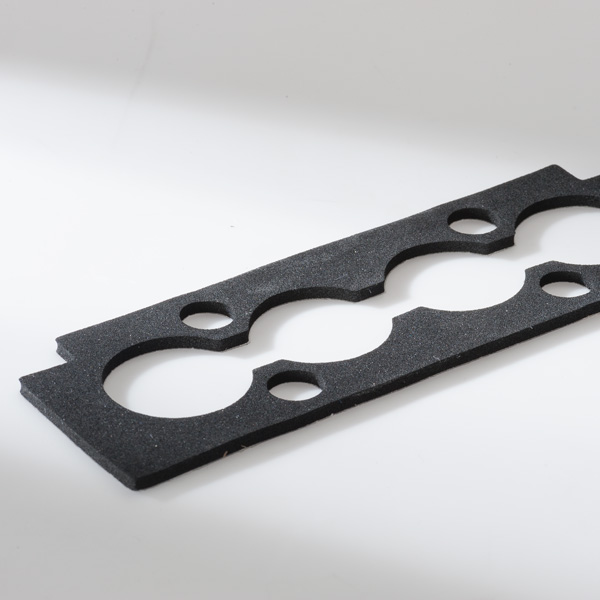
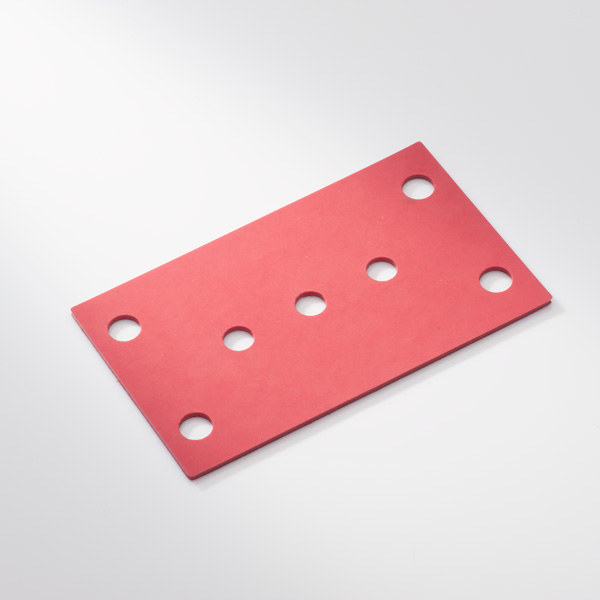
Production of plastic and rubber punched parts
Punching is a non-machining cutting process. The material is severed in this process. Tools that exactly correspond to the desired shape and size of the punched parts are used for processing. During the punching process, the material is clamped between two tools and severed by a punch that moves down to a counterpart called the die. The edges of the die and punch are absolutely parallel to each other. At the start of the punching process, the material is deformed by the contact with the punch before it is cut and finally breaks due to the high tension forces at the cutting contour.Punching is a non-machining cutting process. The material is severed in this process. Tools that exactly correspond to the desired shape and size of the punched parts are used for processing. During the punching process, the material is clamped between two tools and severed by a punch that moves down to a counterpart called the die. The edges of the die and punch are absolutely parallel to each other. At the start of the punching process, the material is deformed by the contact with the punch before it is cut and finally breaks due to the high tension forces at the cutting contour.Materials in use
Various materials can be used for the production of plastic punched parts. The most common materials range from rubber to plastics. We mainly use cellular polyethylene, cellular rubber, foam rubber, NR/SBR, silicone, butyl, HPDE and EPDM/SBR as well as CR in production. Other materials required by you can also be used on request. In combination with various processes and manufacturing operations for the production of punched parts, we offer a broad portfolio. Realising highly complex assemblies is possible thanks to different joining technologies. We therefore offer you complex solutions for all your rubber and plastic punched parts.Benefits of producing rubber punched parts
The benefits of punching are extensive. First among these is the ability to offer a variety of contours and transformations of the plastic and rubber punched parts. Since there are no thermal influences on the material, the quality remains consistent even at large quantities. This leads to the additional benefits of economical and flexible production.
Leading applications
In addition to the usual feedstock, we also work with foamed materials to produce a wide variety of rubber and plastic punched parts. These parts can be used for many different purposes, for example rattle and vibration prevention but also for sealing, damping, insulating, as spacers and in numerous other applications.
Sample applications:· Rattle prevention
· Vibration protection
· Sealing· Damping
· Padding
· Spacers
· Covers
· InsulationExamples of the materials used:
· NR/SBR
· NR/SBR
· EPDM/SBR
· NBR/SBR
· CR
· Silicone
· Butyl
· HPDE
· Cellular polyethylene
· Cellular rubber
· Foam rubber
· And many moreOur products
The precision parts are as different as their applications. Consistent management and exact quality control ensure the required precision in production. Our products distinguish themselves with consistent quality and reliable performance. As your competent partner, we expertly produce plastic and rubber punched parts with great flexibility. The experience of our employees along with our technical knowledge set us and our products apart. We offer a suitable solution whether your order is large or small. In order to meet your needs, we are always working on renewing and expanding our capacities.